A wi-fi community employer has positioned Lean Six Sigma to apply in its business, education a collection of 8 personnel as Green Belts and attaining price financial savings all through the education period. They offer but every other instance of the way Lean and Six Sigma method facilitates organizations reduce waste and discover efficiencies, no matter the industry.
The Pennsylvania-primarily based totally employer, Rajant Corporation, lately released a Lean Six Sigma Green Belt education software for personnel withinside the employer’s workplace in Morehead, Ken. In a information release, employer leaders stated they released this system to educate personnel on doing away with waste and optimizing efficiency “even as maximizing the fee to clients of its merchandise with the bottom feasible investment.”
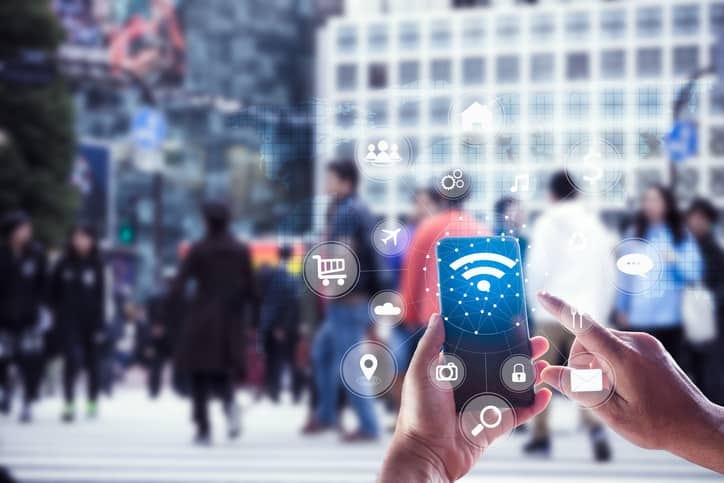
The price financial savings befell all through the Green Belt software as every of the 8 contributors selected to illustrate the effectiveness of various Lean gear in figuring out and correcting operational gaps in quite a few regions throughout the employer’s operations.
They ended up saving the employer $40,000. They additionally ended up with a better, clearer image in their employer’s operations and their function in it.
Lean Training for Wireless Company Employees:
Rajant is a corporation this is very public approximately its dedication to fostering a way of life of non-stop technique development as a manner of assembly patron needs and staying aggressive withinside the wi-fi market.
It makes a speciality of non-public community infrastructure that helps cellular wi-fi communications. To do so, the corporation advanced Kinetic Mesh technology. The corporation has customers in oil and energy, transportation and rail, utilities, telecom, public safety, and government.
Eight personnel primarily based totally in Rajant’s Morehead workplace acquired the Lean Six Sigma education. It concerned engaging in an operational assessment, 5 days withinside the school room for Green Belt education, and 3 days for education in Kaizen.
The 8 personnel discovered the way to make data-pushed selections that concerned statistical techniques discovered at some point of Green Belt education. They centered on placing Lean gear to paintings to reduce waste and meet patron needs, even as that specialize in developing measurable and quantifiable economic returns from their efforts.
Putting Lean Lessons Into Play:
The schooling in Kaizen organized the personnel to end up extrade managers of their region of operation.
The concept at the back of Kaizen is to foster a way of life wherein humans do now no longer withstand extrade and purchase into the concept of non-stop development. Kaizen is a cornerstone for the much-fashionable Toyota Production System. Focused Kaizen events, normally lasting 3 days, are used to discover the foundation reasons of waste in a system and increase methods to get rid of them.
The Rajant personnel did simply that. Each positioned a Lean device to paintings on a hassle as a mission to finish to earn a Green Belt. Added up, the ones financial savings reached $40,000.
They additionally supplied feedback withinside the information launch approximately the fee of Lean schooling. Austin Clark, a structures engineer, stated the schooling “gave me a useful new set of gear and crucial questioning strategies to apply withinside the manner I method my regular tasks.”
He stated he now can view troubles from “a couple of angles,” which guarantees he reveals answers the use of the fine viable device. But the largest extrade is probably the blessings earned withinside the future.
Comments
Post a Comment