What is Operational Excellence?
Operational excellence (OpEx) is the purpose of progressed commercial enterprise performance. It generally manner the usage of lean production techniques, made famous via way of means of Toyota with its Toyota Production System (TPS). For many organizations, OpEx is the set of TPS “tools” that assist remove waste — ‘Muda’ in Japanese terminology — and decrease manufacturing time and costs.
Operational Excellence and Continuous Improvement:
It is frequently assumed that operational excellence is equal to non-stop development. Whilst the 2 are intrinsically linked, there’s a diffused and crucial distinction among those concepts.
At Juran, we outline non-stop development because the want to constantly create ‘breakthroughs’. A step forward can both imply turning in exquisite services and products that generate extra sales and consumer satisfaction, or releasing an employer from failure to lessen consumer dissatisfaction and non-fee introduced waste.
Operational excellence appears past price discount and system enhancements in the direction of the fulfillment of long-time period sustainable growth. It is a attitude that embraces positive concepts and equipment to create a way of life of excellence inside an employer. Operational excellence approach each worker can see, supply and enhance the waft of fee to a consumer.
The Origins of Operational Excellence:
In the early 1970s, Dr. Joseph M. Juran changed into one of the few specialists on the time who changed into coaching Japanese commercial enterprise leaders the way to enhance pleasant. As greater businesses commenced to undertake the techniques of Juran, W. Edwards Deming and others, Toyota’s OpEx motion grew. Today, many production businesses use OpEx as its sole cause to create lean operations.
OpEx commenced withinside the early Nineteen Eighties as a United State reaction to the pleasant crisis. This “crisis” changed into created through Japanese businesses whose merchandise have been outperforming many US and European merchandise, inflicting severa businesses to lose marketplace percentage or even exit of commercial enterprise.
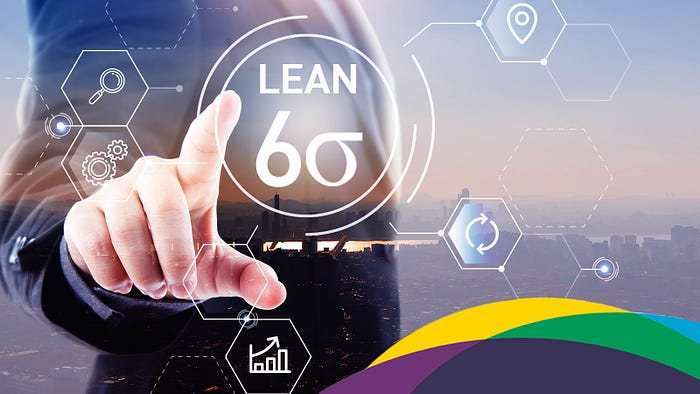
The Core Principles of Operational Excellence:
The foundation of operational excellence is first-class articulated through the Juran and Shingo models.
The Juran Model
The middle additives concepts of Juran’s version for operational excellence are as follows:
1. Grasp Juran’s guiding concepts that lay the muse for excellence.
2. Move your subculture from considering best as a product attribute (little q) to best as a first-rate consumer experience (Big Q).
3. Understand while and the way to interact management and the team of workers to pressure performance.
4. Build an powerful and green alternate infrastructure the usage of the best gear and methods.
5. Drive commercial enterprise system effectiveness and agility.
The Shingo Model
Devised through Dr. Shigeo Shingo, the Shingo Model encompasses ten guiding concepts for operational excellence:
1. Respect each individual — this is applicable to clients, personnel, companions and suppliers. For example, related to all personnel in development tasks and training them on trouble-fixing will lead them to experience emotionally invested of their paintings.
2. Lead with humility — personnel must be empowered to make a contribution thoughts and comments with none worry of repercussions. Leaders must be inclined to are seeking for input, pay attention and learn.
3. Seek perfection — perfection is an aspirational purpose that isn’t possibly to be carried out, however the pursuit of it creates a mind-set and subculture of each non-stop and radical development.
4. Embrace clinical thinking — innovation and development are the result of repeated cycles of experimentation and learning.
5. Focus on system — it could be smooth in charge different human beings for failure, however greater frequently than not, the trouble is the system. A system-led method is fundamental to operational excellence.
6. Assure best on the source — ideal best can simplest be carried out while each detail of labor is accomplished flawlessly the primary time and each time. When and if mistakes occur, they have to be detected and corrected on the factor and time in their creation.
7. Flow & pull price — price for clients is maximized while it’s miles created in reaction to actual call for and a non-stop and uninterrupted waft. Anything that disrupts the non-stop waft of price is waste.
8. Think systemically — information the connection among all elements of a system will assist you’re making higher choices and significant improvements. It’s crucial to dispose of any limitations that save you the waft of thoughts via an corporation.
9. Create consistency of purpose — anybody in an corporation must be aware about its dreams and challenge declaration from day one, with a purpose to align their personal thoughts, movements choices accordingly. This strategic alignment is fundamental for operational excellence.
10. Create price for the consumer — price is described as what a consumer is inclined to pay for. The first-class groups constantly paintings to benefit a deeper information in their clients’ desires and expectations, with a purpose to preserve including price.
Operational Excellence Methodologies:
Knowing the which means and middle ideas of operational excellence is one thing, however the actual mission is reaching it. There are 3 key methodologies that an organisation can also additionally undertake as approach to reaching operational excellence.
Lean ManufacturingThe core focus of lean manufacturing is eliminating waste in a production system, thereby reducing costs. Inspired by the Toyota Production System (TPS), lean manufacturing identifies eight types of waste — or non value-added activities — that must be eliminated if an organization wishes to achieve operational excellence:
Overproduction
Long wait times
Excess transportation
Variable processing methods
Excess inventory
Too much motion
Too many defects
Unused human creativity
Six Sigma
While lean production specializes in waste and price reduction, Six Sigma ambitions to enhance approaches which will create higher products, offerings and price for customers. The methodologies had been historically impartial of 1 another, however from the overdue Nineteen Eighties they had been utilised in concord as Lean Six Sigma, a technique pioneered via way of means of Juran.
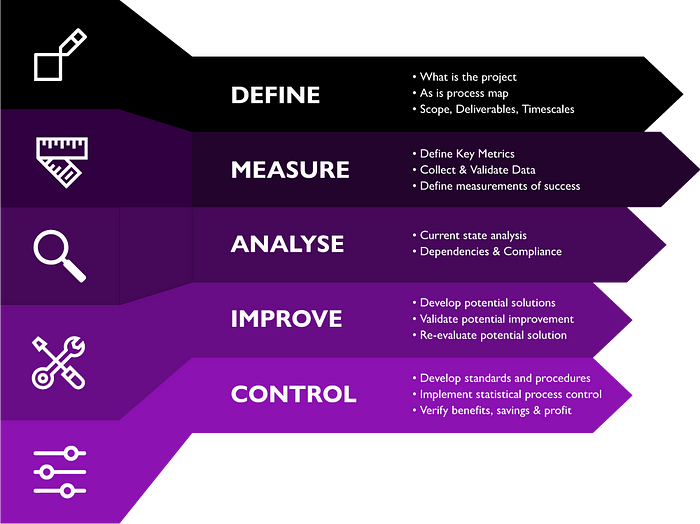
Founded at the general concepts of the Juran Trilogy, Lean Six Sigma presents a complete set of strategies and equipment that assist corporations lessen charges and enhance quality, with the last aim of non-stop price introduction for customers.
Lean Six Sigma development packages comply with a technique referred to as DMAIC, which encompases 5 awesome phases:
Define
Measure
Analyze
Improve
Control
Following DMAIC methodology enables organizations to create ‘breakthroughs’, which ultimately result in sustainable, long-term solutions to any problems identified in the production process.
Kaizen
Kaizen is a Japanese time period that interprets as “alternate for the better”, or “development” to position it simply. In a commercial enterprise context, kaizen is used to explain the incremental enhancements that an business enterprise makes on a every day foundation to assist them create a subculture of non-stop development and consequently gain operational excellence.
Since the 1980s, kaizen has taken on a one of a kind that means withinside the United States, evolving right into a greater established and targeted development pastime referred to as a speedy development occasion (RIE). This established technique to kaizen applies to quality, as properly different parameters consisting of productivity, protection and cycle time. Sporadic troubles are first-rate addressed with a kaizen root purpose corrective action.
A speedy development occasion normally takes among one and ten days to complete, relying on the bottom information and schooling stage of these involved. RIEs additionally require to 3 weeks of extreme making plans previous to execution, encompassing the introduction of an RIE group and charter, identity of key metrics, improvement of a fee movement map, statistics collection, and waste identity.
Comments
Post a Comment